Right now: Start digitizing production simply and benefit quickly
A slump in orders, uncertain supply chains, international wars and conflicts: recent developments have put many companies into “reaction mode”, says KUKA manager Dr. Christian Liedtke, CEO of the Open Industry 4.0 Alliance.
However, according to Dr. Liedtke, strategic planning should not be put off any longer. Right now, especially for medium-sized industrial companies: “Roll up your sleeves and do it!” (Source: Ist der Mittelstand an der Industrie 4.0 gescheitert?)
Digitization greatly increases efficiency potential
Sleeves up – this also applies to the further digitalization of production. Because the key insight in the era of Industry 4.0 and IIoT is that every company today is a software company.
This means that digitalization is also part of the solution in industry and should be launched and expanded quickly as a strategic investment in the future. It is wrong to view digitalization as just an IT project and an expense.
The potential of digital production is huge: processes and supply chains are organized much more flexibly, productivity is increased and costs are optimized. According to McKinsey, digitally controlled production can create enormous added value – for example, 30 to 50% less machine downtime and 15 to 30% higher labor productivity.
According to McKinsey, digitally controlled production can create enormous added value – for example, a 15 to 30 % increase in labor productivity or 30 to 50 % less machine downtime – Source: McKinsey – Link: http://tinyurl.com/2mqfumwj
Laying the foundation – comprehensive connectivity in the factory
The ever faster pace of progress in digitalization no longer allows for any delay. “We will see more technological change in the next 10 years than in the last 50,” U.S. President Joe Biden recently said with regard to artificial intelligence.
At the same time, however, many SMEs still lack a basic prerequisite for digital transformation and smart manufacturing: comprehensive connectivity on the store floor, i.e. a digital connection between machines, manual workstations and sensors.
Even in the third decade of the digital age, it remains a major challenge for manufacturing companies to capture signals from heterogeneous machines and sources, harmonize them and utilize them in downstream systems.
Comprehensive connectivity provides the foundation on which higher productivity can be built:
- Optimized processes and supply chains
- Real-time evaluations on the top floor and shop floor (i.e. in ERP and MES solutions)
- Integration of smart applications such as machine learning, predictive maintenance or AI.
Each factory works with an individual mix of machines, manual workstations, sensors and other sources such as worker input. The foundation for comprehensive digital mapping of production processes is the digital connection of all signal sources and their harmonization in a semantic data model – Photo: Kamran Aydinov auf Freepik
Every factory is different – the ability to integrate is required
In the manufacturing industry, the goals are the same for all companies: sustainability, efficiency, productivity. However, every factory manufactures its own unique products, so the requirements in each factory are different. Each factory works with its own mix of machines, manual workstations, sensors and IT solutions.
The market also demands adaptation: customer expectations are changing faster and faster, more and more individual product variants are desired and production cycles are becoming shorter. “Where to begin?” some production managers ask themselves. And IT managers are asking: “Is there an IT multitool for digital transformation and the smart factory?”
Staying flexible through digitalization
The best response to complexity and rapid change is to remain flexible. Those who are the most adaptable will survive. For the digital transformation of production, this means that integrative and therefore flexible IT platform solutions form a strong backbone today.
- Connectivity solutions for fast data collection and data harmonization – such as our EGDGE CONNECT
- Analysis solutions for real-time evaluations – such as our MES LITE, MES FLEX or E-MES.
Uncovering the treasure in the data lake
In the age of digitalization, data from the shop floor is the source of added value for industry – semantically processed information from machines, sensors, tools and worker input.
This is why connectivity on the shop floor is the only way to discover the real asset of industrial companies, the treasure in the data lake. This is where a digital transformation should start.
Example Siemens Energy: Onboarding for 3,000 heterogeneous machines
Take Siemens Energy, for example. The world’s leading provider of energy technology is relying on FORCAM technology for the digital connection of factory machines at 80 production sites worldwide. The aim of the seven-year project is to digitally optimize production processes at 80 locations using a standardized MES system – through the SAP Digital Manufacturing (SAP DM) infrastructure.
FORCAM is supplying the FORCE EDGE CONNECT platform solution for asset onboarding of up to 3,000 heterogeneous machines for the project. The aim is to generate data from a wide variety of systems – from pressing, milling, punching or turning machines as well as from machines with and without their own software control.
The solution reduces the connection effort for the same machine types to a minimum and provides a semantic data model for comprehensive analyses in SAP DM. All common interfaces are included out-of-the-box (API/MQTT/OPC UA). The project will be launched at five “lighthouse” plants in Germany, the UK and Mexico. A global rollout is then planned.
Video about the EDGE CONNECT solution:EDGE CONNECT Keynote 02 2023 – FORCAM
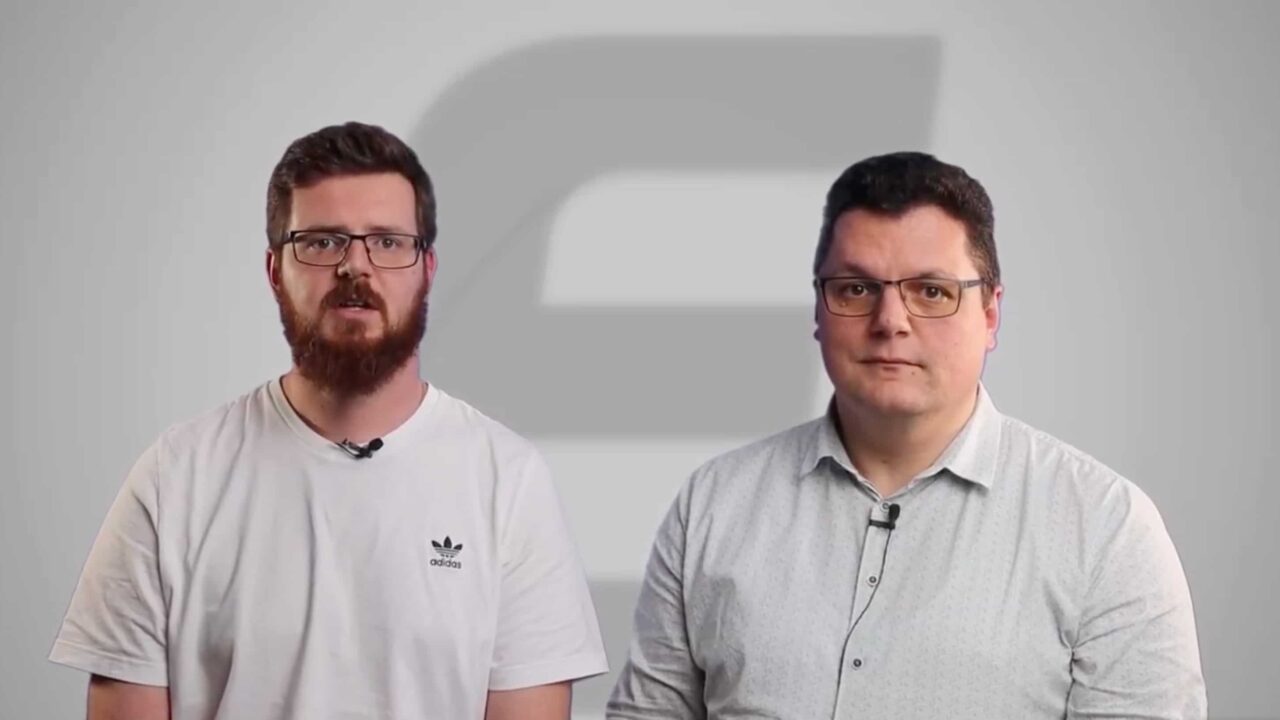
Manual workstations play an important role in contract and individual series production. The digital connection of manual tools such as an Atlas Copco screwdriver using the EDGE CONNECT solution from FORCAM will be demonstrated at the SAP Popup Factory in Walldorf – Photo: SAP
Manual workstations – demo in the “Industry 4.0 Popup Factory” from SAP
In addition to a wide variety of machines, connecting manual workstations digitally is a particular challenge in many places. A demo station in SAP’s “Industry 4.0 Popup Factory” in Walldorf, Germany demonstrates what such a solution looks like.
Production lines for discrete manufacturing and for the process industry are set up in this demo factory. Visitors are welcome to experience the added value of SAP solutions in a realistic store floor environment.
The showcase for manual workstations demonstrates the assembly of an electronic component as an example: At a manual workstation, a person operates a precision screwdriver. The required parts are fed by a robot arm on which a camera is installed.
The screwdriver and robot camera are networked via FORCE EDGE CONNECT. The FORCAM solution generates a data model from the signals and makes it available to SAP Digital Manufacturing for user-friendly virtual inspection of the assembly.
Benefit from digitalization with MES software
Shorter product life cycles, more variants: Companies must respond to this paradigm shift in production with transparency and flexibility. However, both of these efficiency goals can no longer be achieved by physically converting production lines alone. Instead, it is necessary to rely on software with which greater transparency and efficiency can be achieved.
The solution in the era of digitalization and automation is to support lean management methods with modern factory software – a Manufacturing Execution System (MES). The goal of both tools: more efficiency and less waste.
Software first: More transparency and flexibility are achieved today through MES. With tools such as energy monitoring and performance analyses, MES ensure lower costs. Factory teams trained on a high-performance MES can reduce energy and resource costs by a double-digit percentage over the course of a year. Supply chains become more resilient through flexibility. Put simply: If supplier A fails, production must be able to switch to supplier B quickly. This is ensured by an MES.
A continuous flow of data in real time – from the factory to finance – is the goal of successful digitalization of processes on the store floor and the top floor
Conclusion: The need for digitization has never been greater
The need for companies to organize their production digitally has never been greater. Companies should plan their digital transformation in sensible stages. If they want to operate more efficiently, more resiliently and more sustainably, they should put machine connectivity and the associated data semantics at the top of the itinerary.
- The first step: laying the foundations. The benefits of the smart factory can only be fully exploited if heterogeneous machines, manual workstations and sensors are digitally connected.
- The next step is to connect to MES and ERP solutions so that the systems can actually work with real store floor data in real time.
The most important factors for digital transformation are courage and speed. We have known about the possibilities of the internet in industry for 15 years. These must now be exploited.