Gerade jetzt: Digitalisierung der Produktion einfach starten und schnell profitieren
Auftragsflaute, unsichere Lieferketten, internationale Kriege und Konflikte: Die Entwicklungen der jüngsten Zeit haben viele Unternehmen in einen „Reaktionsmodus“ versetzt, urteilt KUKA-Manager Dr. Christian Liedtke, CEO der Open Industry 4.0 Alliance.
Doch strategische Planungen, so Dr. Liedtke, sollten nicht weiter aufgeschoben werden. Gerade jetzt gelte insbesondere für mittelständische Industrieunternehmen: „Ärmel hoch, Ärmel hoch und endlich machen!“ (Quelle: Ist der Mittelstand an der Industrie 4.0 gescheitert?)
Digitalisierung hebt große Effizienzpotenziale
Ärmel hoch – das gilt auch für eine weitere Digitalisierung der Produktion. Denn die zentrale Erkenntnis in der Ära von Industrie 4.0 und IIoT lautet: Jedes Unternehmen ist heute ein Softwareunternehmen.
Das heißt: Digitalisierung ist auch in der Industrie Teil der Lösung und sollte als strategische Investition in die Zukunft zügig gestartet und ausgebaut werden. Falsch ist es, Digitalisierung nur als ein IT-Projekt und Kostenfaktor anzusehen.
Die Potenziale durch digitale Produktion sind groß: Prozesse und Lieferketten werden deutlich flexibler organisiert, die Produktivität gesteigert, Kosten optimiert. Digital gesteuerte Produktion kann laut McKinsey für enorme Wertschöpfung sorgen – zum Beispiel für 30 bis 50% weniger Maschinenstillstände sowie 15 bis 30% höhere Arbeitsproduktivität.
Laut McKinsey kann eine digital gesteuerte Produktion enormen Mehrwert schaffen – zum Beispiel eine um 15 bis 30 % höhere Arbeitsproduktivität oder 30 bis 50 % weniger Maschinenstillstände – Quelle: McKinsey – Link: http://tinyurl.com/2mqfumwj
Das Fundament legen – umfassende Konnektivität in der Fabrik
Die immer schnelleren Fortschritte in der Digitalisierung erlauben keinen Aufschub mehr. „Wir werden in den nächsten 10 Jahren mehr technologische Veränderungen erleben als in den letzten 50 Jahren“, hat U.S. Präsident Joe Biden kürzlich mit Blick auf Künstliche Intelligenz gesagt.
Gleichzeitig aber fehlt in vielen mittelständischen Unternehmen noch eine Grundvoraussetzung für digitale Transformation und smarte Fertigung: eine umfassende Konnektivität auf dem Shopfloor, heißt: eine digitale Anbindung von Maschinen, Handarbeitsplätzen und Sensoren.
Auch im dritten Jahrzehnt des digitalen Zeitalters bleibt es die große Herausforderung in fertigenden Unternehmen, Signale aus heterogenen Maschinen und Quellen zu erfassen, zu harmonisieren und in weiterführenden Systemen zu nutzen.
Umfassende Konnektivität sorgt für das Fundament, auf dem höhere Produktivität entstehen kann:
- optimierte Abläufe und Lieferketten
- Echtzeit-Auswertungen auf Topfloor und Shopfloor (d.h. in ERP- und MES-Lösungen)
- Integration smarter Anwendungen wie Machine Learning, Predictive Maintenance oder KI.
Jede Fabrik arbeitet mit einem individuellen Mix aus Maschinen, Handarbeitsplätzen und Sensoren und weitere Quellen wir Werkereingaben. Das Fundament für eine umfassende digitale Abbildung der Produktionsprozesse ist digitale Anbindung aller Signalquellen sowie deren Harmonisierung in einem semantischen Datenmodell – Foto: Kamran Aydinov auf Freepik
Jede Fabrik ist verschieden – Integrationsfähigkeit ist gefragt
In der fertigenden Industrie sind die Ziele für alle Unternehmen gleich: Nachhaltigkeit, Effizienz, Produktivität. Doch jede Fabrik stellt ihre ganz eigenen Produkte her, entsprechend sind die Anforderungen in jeder Fabrik unterschiedlich. Jede Fabrik arbeitet mit einem eigenen Mix aus Maschinen, Handarbeitsplätzen, Sensoren, IT-Lösungen.
Auch der Markt verlangt nach Anpassung: Kundenerwartungen wechseln immer schneller, immer individuellere Produktvarianten werden gewünscht, Produktionszyklen verkürzen sich. „Wo anfangen?“ fragt sich mancher Produktionsleiter. Und den IT-Chef bewegt die Frage: „Gibt es eine IT-Multitool für die digitale Transformation und die Smart Factory?“
Flexibel bleiben durch Digitalisierung
Die beste Antwort auf Komplexität und schnellen Wandel heißt: flexibel bleiben. Wer am anpassungsfähigsten ist, überlebt. Für die digitale Transformation einer Produktion bedeutet das: Ein starkes Rückgrat bilden heute integrative und damit flexible IT-Plattformlösungen.
- Konnektivitäts-Lösungen für schnelle Datenerfassung und Datenharmonisierung – wie unsere EGDGE CONNECT
- Analyse-Lösungen für Echtzeit-Auswertungen – Wie unsere MES LITE, MES FLEX oder E-MES.
Den Schatz im Datensee heben
Im Zeitalter Digitalisierung sind für die Industrie die Daten aus dem Shopfloor die Quelle für Wertschöpfung – und zwar semantisch aufbereitete Informationen aus Maschinen, Sensoren, Tools und Werkereingaben.
Deshalb führt erst Konnektivität auf dem Shopfloor zum eigentlichen Asset von Industrieunternehmen, zum Schatz im Datensee. Hier sollte eine digitale Transformation ansetzen.
Beispiel Siemens Energy: Onboarding für 3.000 heterogene Maschinen
Beispiel Siemens Energy. Der weltweit führende Anbieter von Energietechnologie setzt bei der digitalen Anbindung der Fabrikmaschinen an weltweit 80 Produktionsstandorten auf FORCAM Technologie. Ziel des auf sieben Jahre angelegten Projektes ist, die Produktionsprozesse an 80 Standorten durch ein standardisiertes MES-System digital zu optimieren – durch die Infrastruktur SAP Digital Manufacturing (SAP DM).
Für das Projekt liefert FORCAM die Plattformlösung FORCE EDGE CONNECT zum Asset Onboarding von bis zu 3.000 heterogenen Maschinen. Es gilt, Daten aus unterschiedlichsten Anlagen zu generieren – aus Press-, Fräs-, Stanz- oder Drehmaschinen sowie aus Maschinen mit und ohne eigene Softwaresteuerung.
Die Lösung reduziert den Anbindungsaufwand bei gleichen Maschinentypen auf ein Minimum und stellt ein semantisches Datenmodell für umfängliche Analysen in SAP DM bereit. Alle gängigen Schnittstellen sind out-of-the-box enthalten (API/MQTT/OPC UA). Gestartet wird an fünf sogenannten Leuchtturm-Werken in Deutschland, Großbritannien und Mexiko. Anschließend ist der weltweite Rollout geplant.
Video zur Lösung EDGE CONNECT: EDGE CONNECT Keynote 02 2023 – FORCAM
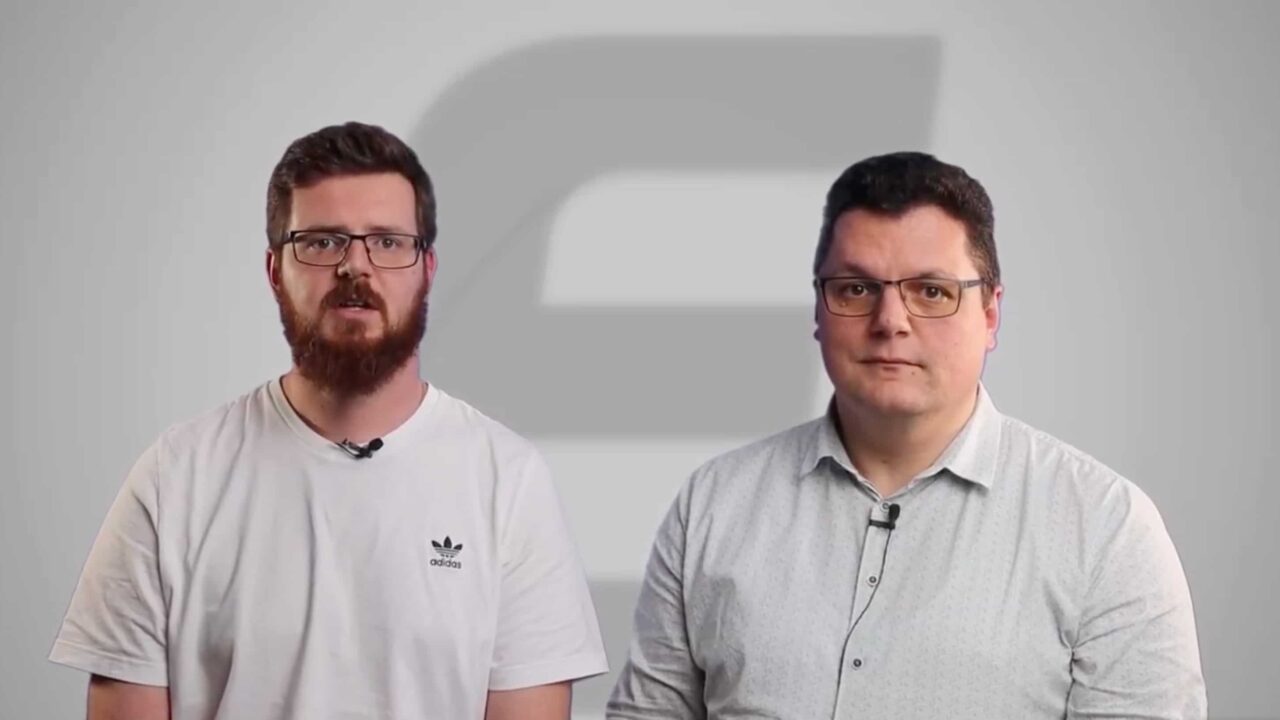
Handarbeitsplätze spielen in der Auftrags- und Einzelserienfertigung eine wichtige Rolle. Die digitale Anbindung von manuellen Tools wie eines Atlas Copco Schraubers durch die Lösung EDGE CONNECT von FORCAM wird in der SAP Popup Factory in Walldorf gezeigt – Foto: SAP
Handarbeitsplätze – Demo in der „Industry 4.0 Popup Factory“ von SAP
Neben unterschiedlichsten Maschinen gilt vielerorts als besondere Herausforderung, Handarbeitsplätze digital anzubinden. Wie eine solche Lösung aussieht, demonstriert eine Demo-Station in der „Industry 4.0 Popup Factory“ von SAP in Walldorf.
In dieser Demo-Fabrik sind Produktionslinien für die diskrete Fertigung und für die Prozessindustrie aufgebaut. Besucher sind willkommen, um den Mehrwert von SAP-Lösungen in einem realistischen Shopfloor-Umfeld zu erfahren.
Der Showcase für Handarbeitsplätze demonstriert exemplarisch die Montage eines elektronischen Bauteils: An einem Handarbeitsplatz bedient ein Mensch einen Präzisionsschrauber. Die benötigten Teile werden von einem Roboterarm zugeführt, auf dem eine Kamera installiert ist.
Schrauber und Roboterkamera sind durch FORCE EDGE CONNECT vernetzt. Die FORCAM Lösung generiert aus den Signalen ein Datenmodell und stellt es dem SAP Digital Manufacturing für die nutzerfreundliche virtuelle Inspektion der Montage bereit.
Mit MES-Software von der Digitalisierung profitieren
Kürzere Produkt-Lebenszyklen, mehr Varianten: Diesem Paradigmenwechsel in der Produktion müssen Unternehmen mit Transparenz und Flexibilität begegnen. Beide Effizienz-Ziele sind heute allerdings nicht mehr allein durch physikalischen Umbau von Produktionslinien zu erreichen. Vielmehr ist es nötig, auf Software zu setzen, mit der höhere Transparenz und Effizienz zu erreichen sind.
Die Lösung in der Ära von Digitalisierung und Automatisierung lautet: Die Methoden des Lean Managements müssen mit moderne Fabriksoftware – einem Manufacturing Execution System (MES) – unterstützt werden. Ziel beider Werkzeuge: mehr Effizienz und weniger Verschwendung.
Software first: Mehr Transparenz und Flexibilität werden heute durch MES erreicht. MES sorgen mit Tools wie Energiemonitoring und Leistungsanalysen für niedrigere Kosten. Fabrikteams, die auf einem leistungsstarken MES geschult sind, können die Energie- und Ressourcenkosten auf Jahressicht im zweistelligen Prozentbereich senken. Widerstandsfähiger werden Lieferketten durch Flexibilität. Einfach gesprochen: Wenn Lieferant A ausfällt, muss die Fertigung schnell auf Lieferant B umstellen können. Dafür sorgt ein MES.
Ein durchgängiger Datenfluss in Echtzeit – von der Fabrik bis zu den Finanzen – ist das Ziel erfolgreicher Digitalisierung von Prozessen auf dem Shopfloor und dem Topfloor
Fazit: Nie war die Notwendigkeit einer Digitalisierung größer
Nie war die Notwendigkeit für Unternehmen größer, ihre Produktion digital zu organisieren. Unternehmen sollten die digitale Transformation in sinnhaften Etappen planen. Wollen sie effizienter, resilienter und nachhaltiger wirtschaften, sollten sie die Maschinen-Konnektivität und die dazugehörige Daten-Semantik ganz oben auf den Reiseplan setzen.
- Der erste Schritt: das Fundament legen. Nur, wenn heterogene Maschinen, Handarbeitsplätze und Sensoren digital angebunden sind, lassen sich die Vorteile der Smart Factory umfänglich nutzen.
- Der nächste: Dann können die Anbindung an MES- und ERP-Lösungen folgen, damit die Systeme tatsächlich mit echten Shopfloor-Daten in Echtzeit arbeiten können.
Dabei am wichtigsten für die digitale Transformation: Mut und Schnelligkeit. Seit 15 Jahren wissen wir um die Möglichkeiten des Internets in der Industrie. Die müssen jetzt genutzt werden.